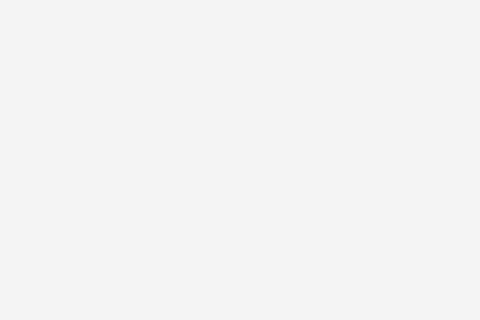
Imagine being able to build a home on a piece of land and reduce your timelines by six to 12 months, save 50 to 80 percent in debt service and lower your construction costs by roughly 15 percent. This is exactly what Richard Palumbo, vice president and co-owner of Custom Modular Designs, LLC, in Rhode Island, says you can expect by using modular home construction.
This underused and often misperceived housing strategy can not only lower costs and reduce timelines, but it may also lower risk with a controlled environment, raise home quality and increase energy efficiency.
Misconceptions
Because modular homes are partially produced in factories, they are sometimes confused with mobile homes or manufactured homes, which are also produced in factories.
“A modular home, contrary to some common belief, is not a mobile home, not a trailer home and it’s not a HUD home. It’s not a panelized home or a kit home,” Palumbo said. “A modular home is a system built product that is…designed in accordance with state and local building codes, and then built in sections, boxes or modules.”
“The modular home is a home that is…the same that would be built on site, but it’s built off site and then moved to the site in sections,” Paul Lewakowski, president and owner of Lionheart Development, a custom modular contractor based in New Orleans, said.
Roughly 70 to 85 percent of a modular home is produced in a controlled factory environment. The boxes are then shipped on trucks and assembled at the home site using a crane. Once assembled, the home is permanent; it is not moveable in the way that mobile homes are.
Unlike mobile homes, modular homes are regulated by the same authorities as traditional site or stick built homes, Lewakowski said.
Modular homes are built to Uniform Building Code (UBC), a higher standard than the HUD code that regulates mobile homes, Rory Manning of Western Finance/Land Home Financial Services, a modular and mobile home lender based in Colorado, said.
Modular home codes call for better plumbing, electrical, floor joisting, wall framing and roof trusses, and they allow for higher roof pitch elevations, Manning said. Modular foundations are also much more sound than mobile home foundations, he said.
Construction speed
Modular homes can be constructed much faster than site or stick built homes. Typically, from the time the home is ordered, “our factories will be able to produce and deliver the home within four to 12 weeks,” Palumbo said.
“We average roughly a 48-day turnaround on a ranch or a Cape Cod style home where the upstairs is available, but it is not finished from the factory,” while a traditional site or stick built home would take six to 12 months, Tim White of Carolina Country Homes, Inc. in South Carolina, said. A two-story modular home would take 60 to 75 days, he said.
The big advantage of fast construction is that “if you’re an investor or a builder or a developer and you’re borrowing money…you’re not paying interest for six months or 12 months,” Palumbo said. “Instead you’re paying interest probably for a period of one to three months.”
In addition to providing savings on interest, a short construction time allows for a faster reaction to market demand. A developer who uses modular construction will likely have a finished product available for rent or purchase before competitors who are using on-site construction.
Construction costs
Not only is modular construction faster than on-site construction, it is also less expensive.
Costs in the New Orleans area are typically 20 percent less than site building, Lewakowski said. Modular construction is particularly cost efficient in areas that are rebuilding after Hurricane Katrina because of the high cost and short supply of labor and materials for on-site rebuilding, he said. (For more information on investing in areas affected by Hurricane Katrina, see our article on investing in the GO Zone.)
“The rule of thumb is that modular construction will be about 85 percent of stick built cost,” Manning, who specializes in the Colorado market, said.
“The delivered price can be as low as $45 to $50 per square foot; however, a finished modular in rural Kansas might be $70 to $80 per foot, while the same home in California could be double that or more,” Manning said.
Claim up to $26,000 per W2 Employee
- Billions of dollars in funding available
- Funds are available to U.S. Businesses NOW
- This is not a loan. These tax credits do not need to be repaid
In the Northeast, the modular portion of a home would be $55 to $75 per square foot, Palumbo said. Using his company’s “assist-you-build” program, the cost for a finished product would be $90 to $125 per square foot, he said. “That’s compared to $150 to $200 a square foot in stick or site construction.”
In South Carolina, costs for a ranch style modular home range from $65 to $90 per square foot, with delivery, setting the home on its foundation, steps and decks, heating and air, electrical, water and sewer connections and building permits included in that cost, White said. In the larger homes of 1,600 to 2,200 square feet, he estimated that his company’s prices are anywhere from $10 to $35 per square foot less than site building costs.
Appraisal and financing
Modular homes’ appraisals, insurance, rents, appreciation and resale values are similar to stick built homes. “My personal feeling is that the resale value of modular homes will eventually…surpass that of stick and site built because of the quality that goes into them,” Palumbo said.
“We offer identical loan programs for modular and stick built homes. Rates, terms and qualifying are the same,” Manning said. “However, construction loan costs for modular construction [are] typically less because the construction period is shorter and fewer draws and inspections are required.”
Because modular homes are constructed so much faster than site or stick built homes, the loan dispersement process is structured differently. In traditional construction, the loan is dispersed in phases as major elements of the construction process are completed, Lewakowski said.
In modular construction, “everything happens so much faster that by the time the construction loan comes out, the house is finished,” he said. Banks have adjusted to this process and will now provide about 35 percent up front for the foundation and building of the house, and then will pay the rest once the home is delivered, he said.
At first, the lending industry resisted providing fewer, larger payments, but Palumbo said he has “seen a huge change in the last four years…more and more mainstream lenders are eager to work with modular builders.”
Delivery costs and limitations
Modular homes or buildings can be delivered to almost any property, with a few limitations. “There [are] very, very few properties we can’t place a house on because the crane people…are fantastic,” Lewakowski said.
“On occasion you’ll find a lot or a location that’s not accessible; it typically comes down to the width of the road,” Palumbo said. “You need a pretty standard size width on a road; 15 feet is pretty much a minimum.”
Height is also a restriction, Lewakowski said. “It used to be you couldn’t do 10-foot ceilings on a single story house or 10-foot ceilings on a second story house….Now you can do anywhere from eight- to 10-foot [ceilings] on a single story or the second story of a house.”
Delivery cost varies from location to location, White said. “It just depends on how far the delivery is from the factory where the home is constructed. The factory charges the delivery rates…depending on the mileage.”
If the load is within a standard size of 13 feet, 9 inches or less, costs will be lower than if it is oversized—up to 15 feet, 9 inches, Palumbo said. “If it’s oversized, you need a transport vehicle and in some states a police escort….That will affect costs.”
However, “usually, good designs can eliminate the need for oversized boxes,” Palumbo said. Difficult areas such as mountains and islands can increase costs, but the cost of building in those areas is already inflated, “so the little bit of extra shipping cost typically is not cost prohibitive to the overall project,” he said.
A controlled environment
“What was appealing to a customer…and what was appealing to a developer on my end, was just that you’re taking so much of the risk out of the game,” Lewakowski said. Factory production means fewer accidents and mistakes and a more predictable product and time frame, he said.
The controlled environment also eliminates the common problem of “sick building syndrome” or toxic mold because the material is never wet, snowed on or rained on, Palumbo said.
Modular homes offer a much higher quality control standard, with so many third-party inspectors, engineers and architects involved, Lewakowski said. “For example, when they build the deck of a modular home…their machinery will physically lift that whole deck up, and they’ll look under the deck to see if any nails were missed….They’ll make sure everything is done perfectly.”
Higher quality is standard in modular homes because they must be sturdy enough to travel down the road on a truck after factory assembly, Lewakowski said. They must also be lifted by a crane once they arrive at the site, White said.
Modular homes routinely use energy efficient windows, two by six rather than two by four construction and 40 percent more insulation in the walls, Palumbo said.
“You’re ending up with a very, very efficient home,” Lewakowski said.
“You typically have 30 percent more material that goes into the home with 30 percent less waste,” Palumbo said.
Not surprisingly, “green” modular homes for sustainable living using renewable products and resources are growing in popularity, Palumbo said. The green products are 10 to 20 percent higher in cost than regular modular homes, not including the cost of solar panels, but they are becoming more and more cost effective, he said.
“It’s definitely the direction of the market—high efficiency, green living, renewable resources,” he said.
Designs and strategies
Most modular companies offer a limited number of designs, although custom modular companies offer nearly an unlimited number of options. Modular construction can be used for single family, multi-family and even commercial buildings.
Of the single family home designs, a ranch style home of 1,600 to 2,200 square feet is probably the most cost effective per square foot, White said.
Multi-family modular construction offers an especially interesting investment opportunity because of the speed of construction and the return on investment. “There’s really not much difference in the cost per square foot of a delivered unit between multi-family and single family,” Manning said.
The fast construction process means multi-family developers can receive three to six months of additional rent. For a property with four units renting at $700 per month each, that would be between $8,400 and $16,800 extra from the start, along with savings in debt service and savings of approximately 15 percent on construction costs.
The additional elements of multi-family that local building codes require, such as smoke detectors, carbon monoxide detectors, sprinklers and fire stopping and blocking between units, are easier and cheaper to install in a factory, Palumbo said.
Like stick built multi-family buildings, modular products can go up to three stories high without using steel, Lewakowski said.
Although there is no special licensing or certification for a builder to build a modular home, multi-family or commercial building other than the state regulations that also apply to stick builders, most reputable modular dealers and builders should have extensive factory and independent association training and/or certification, Palumbo said.
In addition, high volume modular dealers will have relationships with numerous factories, providing a greater selection of options and lower prices, Palumbo said. In most cases, the dealer’s cost for setting the building on the foundation is included in the price of the modular building, but most factories either do not offer or can not adequately coordinate the set and installation of the product on the foundation, he said.
“People that are doing multi-family [modular] are loving it because…their risk is controlled, their time is controlled, they know what they’re going to get and they know when it’s going to come and it’s not going to take forever,” Lewakowski said.
Resistance to modular homes
Most cities or neighborhoods that resist modular homes don’t really understand what modular homes are. “In the past, the industry itself has met some resistance, primarily because people confuse and sometimes building officials confuse the difference between modular or mobile or trailer park type of homes,” Palumbo said.
However, public perception is quickly changing, and the stigma of factory built homes is disappearing because the quality of construction has increased so much over the last few years, Manning said.
In fact, it has become impossible for most people to tell by looking whether a home was built modularly or on site, he said.
“In today’s world, most building officials and cities and states and zoning boards are very familiar with the modular product,” Palumbo said. “Most of them enjoy working with it because it eliminates the amount of work that they have to do because…the modular product is actually inspected by a second party or third party inspection company right at the factory.”
Modular construction is fairly new to the New Orleans area, Lewakowski said. When modular was first introduced, “nobody was very familiar with it, and they had the misconception [that] it’s of a lower quality and we’re not going to keep our same architecture,” he said.
By using custom modular and local architects, his company helped to change perceptions of modular homes in the New Orleans area and even convinced some cities to change their laws about modular homes, Lewakowski said.
“It’s almost like switching from a coal engine into a gas or diesel engine,” Lewakowski said. “Things change. It’s a new way of building.”